Competency-Based Assessments for Today’s Advanced Manufacturing Technicians
In 2012 Nocti Business Solutions conducted a study on behalf of AMTEC to identify what industry experts needed from their future Maintenance Technicians. Through the study, NBS worked closely with industry leaders to create the modules, lessons, and labs, that are used in today’s AMTEC program. In 2016 a Delphi study was conducted to keep the original assessment up to date.
How was the General Mechatronics Assessment Created?
In 2007, AMTEC developed a comprehensive list of occupational standards through a DACUM. The occupational standards were identified using the following steps:
Used the subject matter experts to identify the standards
+
–
In September 2007, the AMTEC standards were developed by subject matter experts in the classification of Multi-Skilled maintenance technicians at the Toyota Motor Manufacturing plant in Georgetown, KY. The subject matter experts represented maintenance technicians from various automotive companies including Toyota, Ford and General Motors. These subject matter experts came from different departments including building facilities, stamping, plastics, paint, body-weld, power train, and assembly. All of the experts were actual workers — not supervisors or trainers. The experts were asked to detail the tasks they actually perform on their job.
Collected details and work enablers
+
–
For example, one of the maintenance standards identified was “Troubleshooting/repairing/replacing brakes and clutches.” However, the Turbo-DACUM process collected specific details about the task by asking the subject matter experts to identify specific work performed on brakes and clutches and provides details such as inspecting the breaks for wear and disassembling the disks and pads.
Identified work enablers required to perform each standard
+
–
All occupational standards or tasks require enabling content knowledge or skills to be effectively performed. Therefore, the Turbo-DACUM process used the subject matter experts to identify the following work enablers:
- Tools and Equipment: What types of tools and equipment are needed to perform this task, and what skills do maintenance workers need to operate these tools and equipment?
- Calculations: What calculations are required to perform this task, and what math skills are required to perform these calculations?
- Communications: How much does the maintenance worker communicate with others to perform this task, and what communication skills are required to do so?
- Technology: What technology is needed to perform this task, and what technological skills must the worker have in order to do so?
- Safety: What safety practices are associated with performing this task, and what knowledge of safety practices must the maintenance work know in order to successfully accomplish this task?The result of the process is a comprehensive set of 26 “duty areas” and more than 170 occupational standards in the form of detailed and task statements of actual work performed.
Weighted the importance of each duty area and rated the criticality of each occupational standard by plant
+
–
AMTEC partners and AMTEC educational institutions operate in different ways across state lines. Therefore, AMTEC used an electronic Delphi process to have each industrial partner weight the duty areas and rate the standards for their specific application and plant needs. This analysis provides the educational partners in a local region the ability to customize their work to meet their specific needs. Such knowledge gives the local college a tremendous amount of information about how the local plant operates and hence, how to emphasize or de-emphasize the different standards in their region.
Synthesized data to develop a “core” set of standards for all partners
+
–
In August, 2008, AMTEC conducted a workshop where industry partners along with college partners, systematically analyzed the data from the Delphi to create a “core” list of occupational standards. The core standards include approximately 20 duty areas and 100 task-based standards.
In 2009 AMTEC contracted with Occupational Research & Assessment (ORA) to conduct a three-round Delphi study of the technical standards. The Delphi process included an electronic survey process to re-validate these occupational standards developed in 2008 with a larger group of industry sectors, employers and faculty. The Delphi method has been widely used to generate forecasts in technology, education, and other fields. It is based on a structured process for collecting and distilling knowledge from a group of experts by means of a series of questionnaires and is a technique similar to focus groups. Its value is that unlike focus groups, Delphi groups do not have to physically meet. The Delphi technique is a method of generating ideas and facilitating consensus among individuals who have special knowledge to share, but who are not always in contact with each other.
General Mechatronics Assessment Breakdown
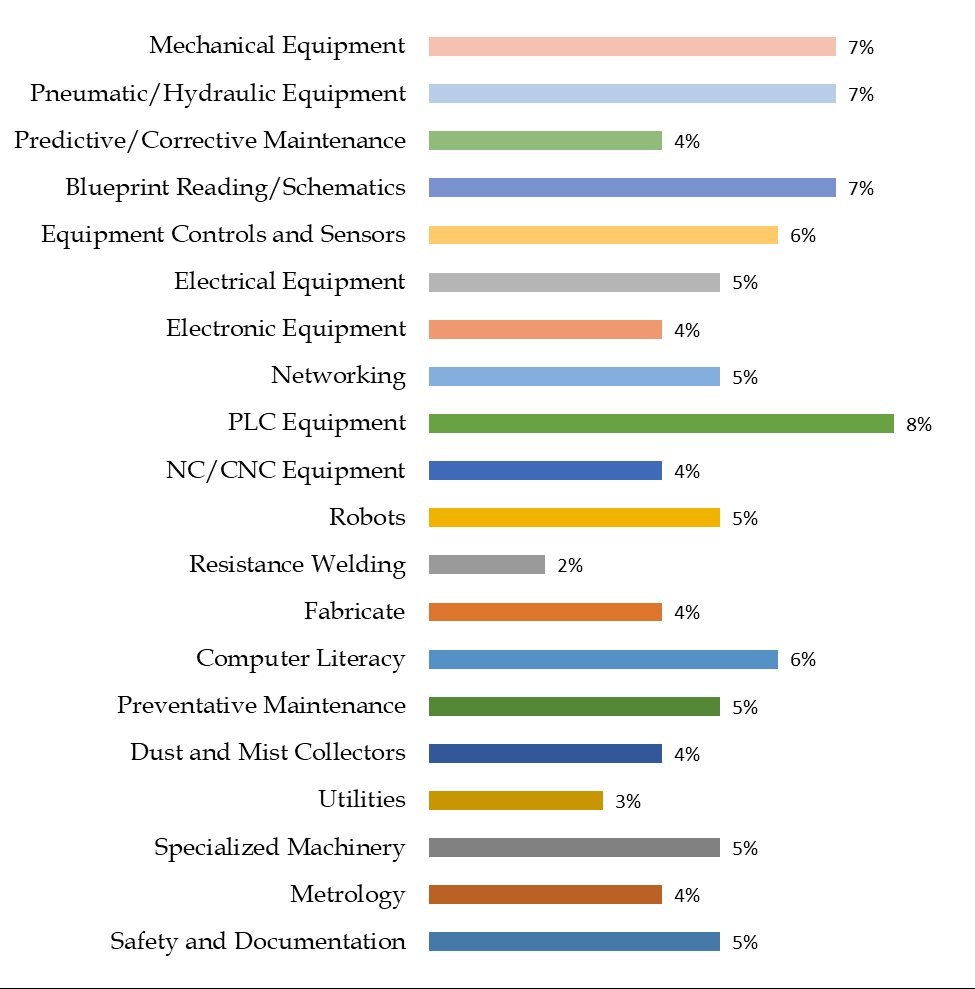
For a more detailed description of the General Mechatronics Assessment click HERE to download the blueprint.
How is the General Mechatronics Assessment being used?
The General Mechatronics Assessment is being used in a variety of ways across the country:
- Boeing facilities in the Puget Sound area use the assessment as a pre-hire tool. The national cut score has to be met on the assessment in order for a candidate to be considered.
- TTNA (Toyotetsu North America) uses the assessment to test incumbent workers to develop a baseline and then offers incentives to them to upskill. If they complete training and demonstrate improvement after a set period they are promoted and given pay increases.
- Honda Manufacturing of Indiana is coming on as a partner to use the assessment to first test incumbent workers, and depending on their score give them pay increases. Then, moving forward, all new hires will be given the assessment and if they score high enough they will start at a higher pay grade. They are hoping this will help them recruit technicians that are more experienced.
- Workforce development agencies across the country utilize it to test a companies maintenance staff to identify skills gaps, then customize training according to the results.
- Colleges use it to test incoming students to establish a baseline, then test them at the end of the program to prove competency in the learning outcomes.
- All KCTCS schools across KY use the assessment as an end of program assessment for all IMT and AMT programs.
- This is also AMTEC’s credentialing assessment. If the national cut score is met, the individual earns a certificate indicating that they have shown mastery of general mechatronics according to industry guidelines. There is a Level 1 and Advanced Level 2 certificate, that comes with a digital badge that can be shared on social media as well as attached to electronic copies of resumes.
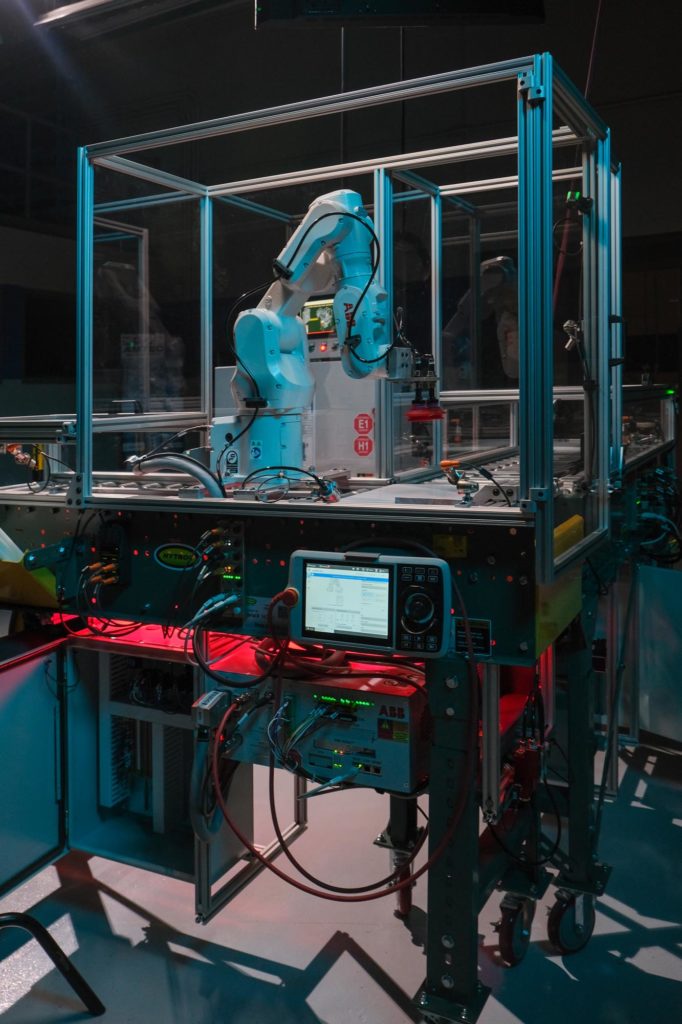
To become an AMTEC approved testing site and for more information contact us.